15 Reasons Why the Best Press Machine Can Transform Your Production Process
In a rapidly evolving industrial landscape, the demand for efficiency and precision in production processes has never been higher. According to a recent report by Mordor Intelligence, the global press machine market is projected to reach USD 10.5 billion by 2025, growing at a CAGR of 5.6%. This growth is fueled by advancements in technology and the increasing need for automated solutions across various sectors. A high-quality press machine not only enhances production capabilities but also significantly reduces operational costs and improves product quality.
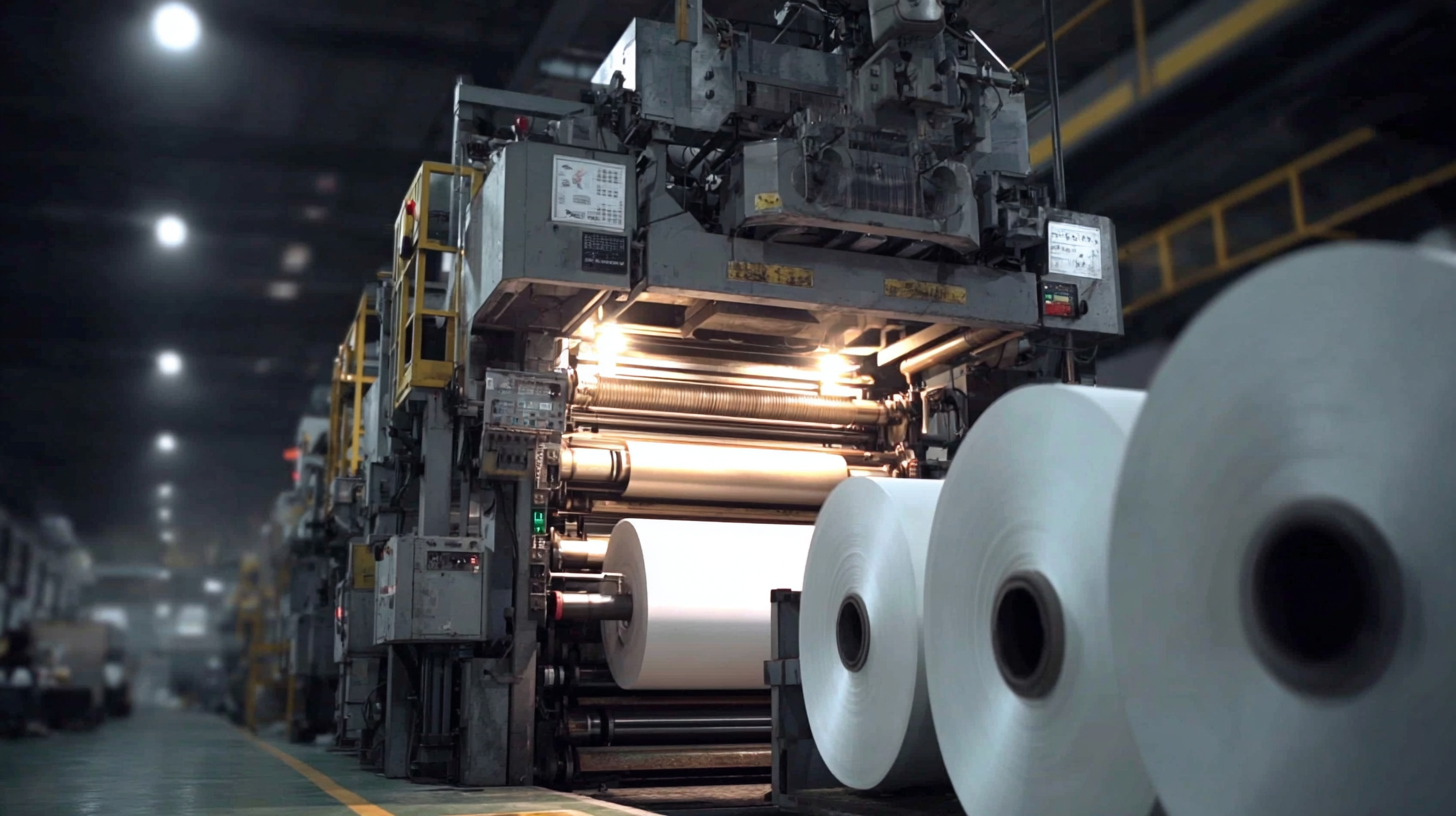
In this blog, we will explore 15 compelling reasons why investing in the best press machine can revolutionize your production process, driving efficiency and innovation in your operations. As industries aim for sustainability and higher productivity, the right press machine becomes an essential tool for maintaining competitive advantage and meeting customer demands.
Key Features of Top Press Machines That Revolutionize Production
When it comes to enhancing production efficiency, the features of top press machines play a crucial role. One of the key attributes is precision. Advanced press machines are equipped with state-of-the-art technology that ensures
every operation is executed with high accuracy, reducing material wastage and increasing product quality. Additionally, automation capabilities allow these machines to operate continuously without significant downtime,
drastically improving productivity levels.
Another vital feature is flexibility. Modern press machines can handle a wide range of materials and product specifications, enabling manufacturers to adapt to market demands quickly.
This versatility means that businesses can scale production up or down without investing in new equipment every time production needs shift.
Tips: When selecting a press machine, consider investing in models that offer integrated software solutions for monitoring and control.
This feature not only streamlines processes but also provides real-time data analytics for informed decision-making. Furthermore, routine maintenance checks are essential for ensuring longevity and optimal performance of your press machine.
Regular maintenance can prevent costly breakdowns and keep production on track.
How Advanced Technology Enhances Efficiency in Press Processes
The advent of advanced technology in press machines has revolutionized production processes, significantly enhancing efficiency. According to a report by the International Society of Automation, automated presses can increase production speeds by up to 50%, reducing downtime and labor costs. A key factor in this enhancement is the integration of smart sensors and data analytics, which allow real-time monitoring of production lines, identifying bottlenecks and minimizing waste. This data-driven approach leads to higher precision, yielding up to 90% fewer defects in the final products.
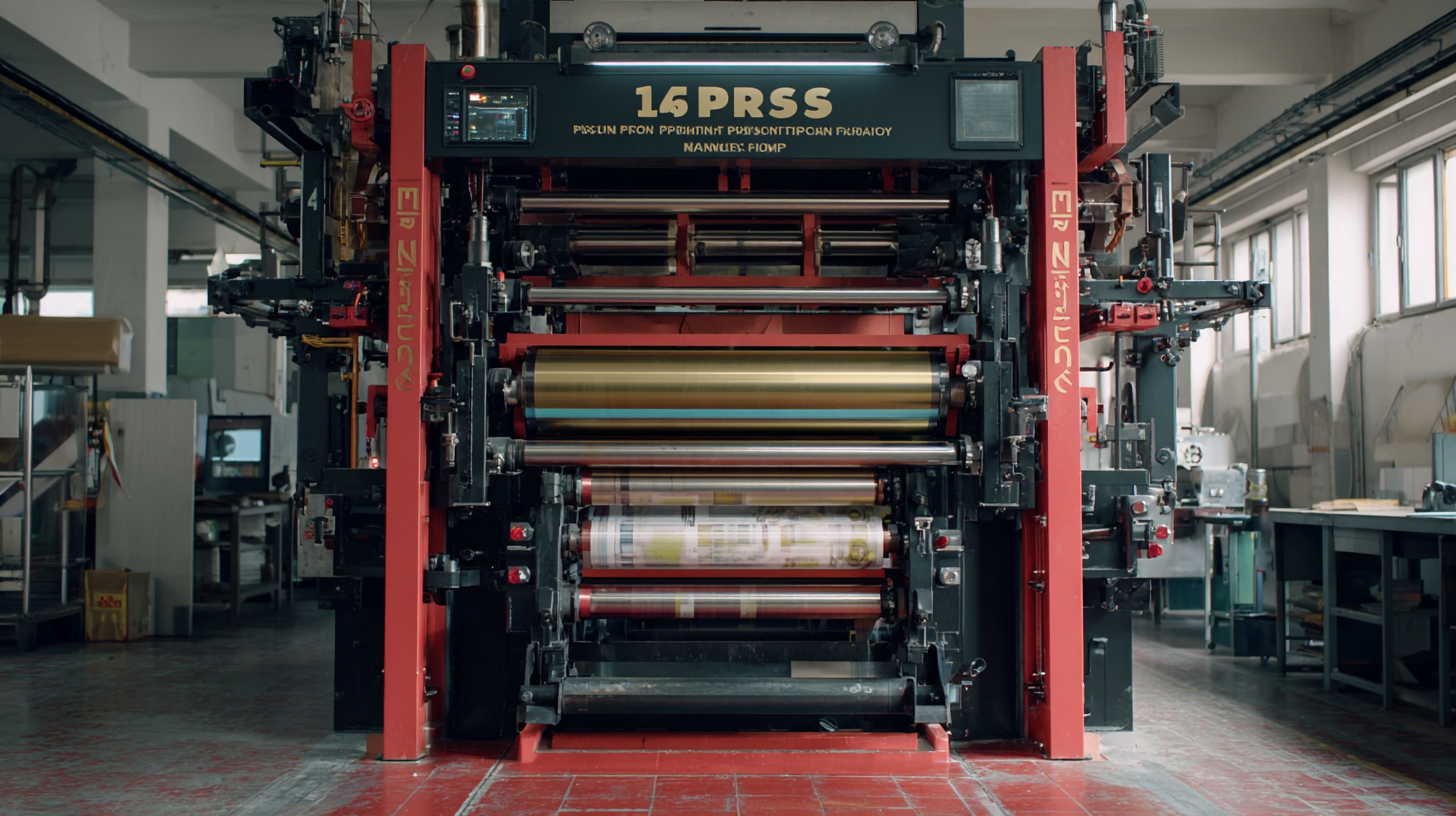
To leverage the full potential of modern press machines, companies should consider incorporating predictive maintenance practices. By utilizing machine learning algorithms, businesses can forecast equipment failures before they occur, which can lead to a reduction in unscheduled downtime by as much as 40%. Additionally, upgrading to presses with adjustable parameters allows for quick changes in production specifications, enhancing flexibility and responsiveness to market demands.
Investing in employee training is equally vital. An experienced workforce that understands the technological capabilities of advanced presses can further optimize production efficiency. Research shows organizations that prioritize training experience a 20% increase in productivity and employee satisfaction. Ultimately, embracing technology not only enhances operational efficiency but also fosters a culture of innovation within the production environment.
Cost Savings: How the Best Press Machines Reduce Operational Expenses
When it comes to optimizing production processes, the implementation of the best press machines can lead to significant cost savings. A report by the Machinery Institute notes that using advanced press machines can reduce operational expenses by up to 20% due to improved efficiency and lower energy consumption. These machines often feature state-of-the-art automation and monitoring systems, minimizing the need for manual adjustments and reducing downtime, which further contributes to financial savings.
**Tip:** Regular maintenance of your press machines ensures they operate at peak efficiency. Implementing a scheduled upkeep routine can help avoid unexpected breakdowns and prolong the life of your equipment.
Moreover, the latest press machines are designed to maximize material use, reducing waste and lowering costs associated with raw materials. According to a study from the Production Analysis Group, companies that upgraded to modern press technology saw a 15% reduction in material waste. This not only leads to direct cost savings but also boosts sustainability efforts, a vital aspect in today’s manufacturing landscape.
**Tip:** Consider training your operators on the latest features of your press machines. Well-informed personnel can leverage all the technological advancements, leading to even greater efficiency and savings in the production line.
15 Reasons Why the Best Press Machine Can Transform Your Production Process - Cost Savings: How the Best Press Machines Reduce Operational Expenses
Reason | Description | Estimated Cost Savings ($) | Impact on Production Efficiency (%) |
---|---|---|---|
Lower Energy Consumption | Advanced technology reduces energy usage. | $2,500 | 15% |
Reduced Labor Costs | Automation leads to fewer necessary staff. | $5,000 | 20% |
Minimized Waste | Precision features reduce material waste. | $3,200 | 10% |
Faster Production Speed | High-speed operation increases output. | $4,000 | 25% |
Lower Maintenance Costs | Reliability leads to fewer repairs. | $1,800 | 8% |
Improved Quality Control | Consistent quality reduces reject rates. | $3,500 | 12% |
Enhanced Safety Features | Advanced safety reduces accidents. | $2,200 | 5% |
Flexible Production Options | Adaptable designs cater to various products. | $2,750 | 15% |
Longer Equipment Lifespan | Investments pay off over time. | $3,000 | 6% |
Improved Scalability | Easily increase production as demand grows. | $4,500 | 18% |
Improving Product Quality: The Impact of Precision Press Machines
The emergence of precision press machines has dramatically revolutionized the production process across various industries. With their ability to deliver consistent and high-quality outputs, these machines ensure that every product meets stringent quality standards. This impact on product quality can be attributed to the advanced technology embedded in these machines, allowing for precise control over dimensions and material properties. When manufacturers invest in top-tier press machines, they not only enhance their product quality but also boost overall operational efficiency.
Automation plays a critical role in this transformation. The rise of CNC technology in manufacturing has led to significant advancements, enabling faster production cycles and reduced labor costs. As automation continues to expand, the demand for precision press machines grows, further driving market expansion. This push towards automation not only streamlines processes but also promotes innovation, ensuring that manufacturers can respond swiftly to market demands while maintaining high-quality standards. Embracing these technologies is essential for businesses aiming to stay competitive in an increasingly automated marketplace.
Streamlining Workflow: Integrating Press Machines in Modern Factories
In an era where efficiency is paramount, integrating advanced press machines into modern factories has become essential for streamlining workflow. According to a report by the International Federation of Robotics, the adoption of industrial robots, including press machines, is projected to grow by 14% annually, highlighting the increasing reliance on automation to enhance production capabilities. These machines not only reduce labor costs but also significantly improve precision and speed, leading to a more agile manufacturing process.
Additionally, a study by McKinsey & Company indicates that companies implementing automated solutions can experience a productivity increase of up to 30%. By integrating state-of-the-art press machines, manufacturers can optimize their workflow, reduce downtime, and minimize errors that often arise in manual operations. This integration facilitates a seamless flow of materials and components, ensuring that production lines maintain momentum and output targets are consistently met. The shift towards automated press machines is not just a trend but a necessary evolution in manufacturing, setting the foundation for future advancements in productivity and efficiency.